摘要:介紹了燒結機頭煙氣中煙粉塵、重金屬、SO2、NOx,以及二惡英的排放現(xiàn)狀。分別從源頭減排、過程控制、末端治理等三方面分析了污染防治技術的應用現(xiàn)狀。根據(jù)燒結煙氣多污染物排放特點及其防控需要,針對不同工藝,提出了4種多污染物聯(lián)合防治技術路線,并分析了其優(yōu)缺點。同時,對燒結煙氣污染物治理的發(fā)展方向進行探討,提出應對燒結煙氣中細顆粒物與重金屬的排放情況和防治技術做進一步研究。
0引言
隨著我國粗鋼產(chǎn)量的逐年增長,鋼鐵行業(yè)大氣污染問題愈加嚴重。燒結作為鋼鐵生產(chǎn)過程中污染最嚴重的工藝環(huán)節(jié)之一,其煙氣治理已經(jīng)成為重中之重。GB28662—2012《鋼鐵燒結、球團工業(yè)大氣污染物排放標準》提高并新增了多污染物排放限值,對燒結煙氣污染物防治提出了更高的要求。
燒結過程煙氣量大,污染物種類多,含量波動大,煙氣溫度低。目前燒結機頭煙氣污染物的治理措施主要分為3個階段:源頭減排、過程控制和末端治理。
源頭減排是在保證燒結礦性能不受影響的前提下,通過對燒結原料中的S、N、礦物元素以及不完全燃燒的碳顆粒物等成分的控制,從源頭上減少煙氣中多種污染物的排放濃度,降低末端治理設備的凈化壓力。
過程控制是在燒結生產(chǎn)過程中進行污染物減排。主要方法是采用煙氣循環(huán)技術,去除煙氣中的多種污染物,減少煙氣和污染物的排放總量,并利用循環(huán)煙氣中的余熱,降低能耗。
末端治理則是采用電除塵器(ESP)、布袋除塵器(FB)和濕法脫硫(WFGD)等凈化設備來脫除燒結煙氣中的各種污染物。為滿足愈發(fā)嚴格的排放要求,必須改造升級化設備,或者更換更高脫除效率的凈化設備。同時,凈化過程產(chǎn)生的廢棄物若處置不當會造成二次污染。
1燒結煙氣污染物現(xiàn)狀
1.1煙粉塵
燒結生產(chǎn)伴隨燃燒過程會產(chǎn)生大量的煙粉塵,未經(jīng)處理的燒結煙氣煙粉塵濃度??蛇_10g/m3左右,其粒徑分級主要集中在100μm的粗顆粒,以及PM10和PM2.5,其中PM10與PM2.5分別占總量的51.23%、43.73%。煙粉塵組分以鐵礦物顆粒、堿金屬礦物顆粒和不完全燃燒物為主,需及時處理,以減小對后續(xù)煙氣凈化設備的影響。
1.2重金屬
燒結機頭煙氣中的多種重金屬,如Pb、Zn、As、Cu、Cr等,主要富集煙粉塵中(圖1)。在凈化過程中,一部分被除塵器捕集,作為返灰配入原料中重新燒結,使得燒結礦中重屬含量增高;一部分經(jīng)由脫硫設備富集在脫硫副產(chǎn)物中,影響其安全利用;剩余部分會隨著煙道排,對周邊環(huán)境造成重污染。較高比電阻的重金屬氧化物,會在電極上形成絕緣層,降低電除塵器的除塵效率,影響正常排灰。
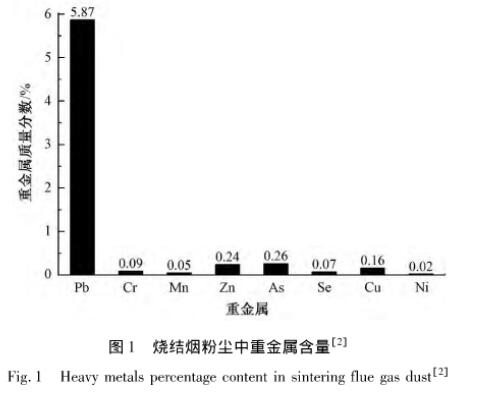
目前,對燒結機頭煙氣的重金屬排放及凈化的研究較少。迫切需要開展煙氣中重金屬含量、度和分布等排放特性研究,也需要開展煙氣凈化設備,例如ESP、FB和WFGD等對重金屬排放量的凈化效果研究,以便為今后重金屬防控提供數(shù)據(jù)基礎。
1.3二氧化硫
燒結機頭煙氣中SO2因燒結原料的配比、鋪料方式、燒結工況等因素影響,波動很大,不同地區(qū)原料不同,差異明顯。我國各地區(qū)燒結機頭煙氣中SO2含量見圖2。
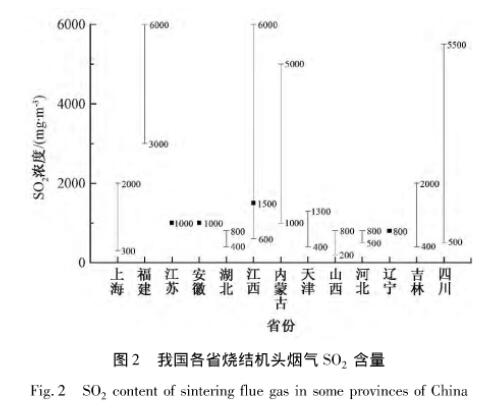
大部分地區(qū)SO2濃度波動范圍小于2000mg/m3,脫硫設備效率達到90%,即可滿足200mg/m3的排放標準,福建、江西和四川等地的SO2濃度波動較大,最高能達到6000mg/m3,對脫硫設備的負荷要求高。燒結杯實驗研究發(fā)現(xiàn),燒結過程中形成的SO2會在燒結料層中進行脫附擴散,但由于過濕帶對SO2有較強的吸附作用,會導致SO2的排放在過濕帶的形成和消失處形成兩個峰值。因此,煙氣中SO2排放量會受燃料量、混合料水分、礦粉含硫量、混合料堿度等因素影響。
1.4氮氧化物
由燒結燃料(煤粉、焦粉)燃燒產(chǎn)生的燃料型NO,占燒結煙氣中NOx的90%以上。見圖3,我國燒結煙氣中NOx含量為100~500mg/m3,波動較大。目前,燒結煙氣脫硝主要以活性炭/焦吸附為主。
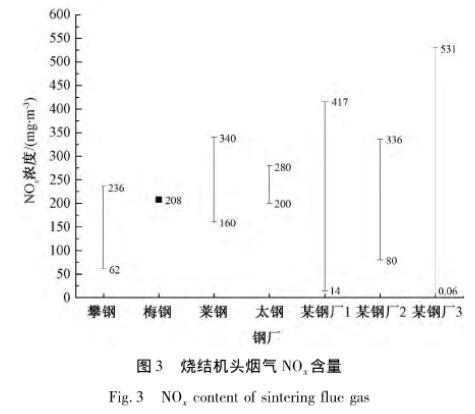
1.5二惡英
燒結過程中的二惡英主要由“從頭合成”途徑生成。燒結原料中含有的Fe、Cu、Cl等元素提供了催化劑和氯源;燃料的不充分燃燒提供了大分子碳源;燒結過程漏風率高,含氧充足,在250~450℃,二惡英的“從頭合成”得以發(fā)生。目前國內(nèi)關于燒結煙氣中二惡英含量的報道較少,如圖4所示,不同燒結煙氣的二惡英排放量差別很大,可能跟原料與工況有關。
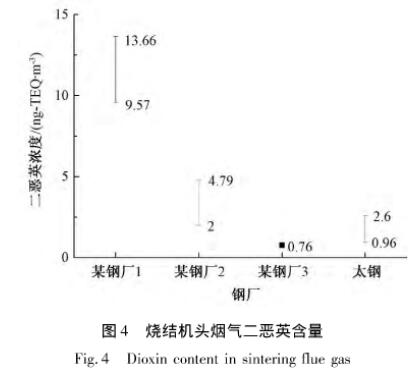
2源頭減排技術
2.1煙粉塵
目前,從源頭減排燒結煙氣粉塵濃度的研究較少。現(xiàn)有燒結機頭ESP在正常運行時,基本滿足脫硫設施入口粉塵濃度要求,但隨著對PM2.5和PM10的關注越來越多,以及ESP存在的細顆粒物穿透窗口問題,使得從源頭減排PM2.5和PM10總量的研究更具環(huán)境效益。
2.2二氧化硫
燒結工藝參數(shù)對煙氣SO2產(chǎn)排有明顯影響。焦粉配比的降低、生石灰配比的增加,可導致SO2排放峰值降低。有研究者利用尿素良好的脫硫能力將其布置在燒結鋪底料上方,發(fā)現(xiàn)煙氣中SO2的排放濃度降到108mg/m3,硫率達到84.4%,且脫硫成本較低。
2.3氮氧化物
NO排放規(guī)律與燒結原料中的N元素含量高低相一致,控制燒結原料中的N元素存在形式,可以很好地控制NOx排放量。有學者通過燒結杯實驗改變混合料含水量、燃料配比、料層厚度、生石灰配比等燒結工藝參數(shù),發(fā)現(xiàn)煙氣中的NO減排量在10%~20%。
2.4二惡英
二惡英源頭減排主要分為兩方面:1)從二惡英的生成機理考慮,應減少Fe、Cu、Cl等元素在燒結原料中的含量,如減少軋鋼氧化鐵皮回用量、混料前洗滌或高溫處理燒結回用料,或者添加抑制劑,如硫酸銨、尿素等減少二惡英的生成量;2)從二惡英的性質考慮,應調整燒結工藝,通過煙氣循環(huán)技術高溫裂解二惡英,減少排放量。
3過程控制技術
3.1能量優(yōu)化燒結技術EOS
EOS技術在燒結機頭煙氣匯集經(jīng)旋風除塵器后,將約50%的煙氣與少量空氣混合,循環(huán)至熱風罩,剩余的煙氣外排處。該技術在利用了循環(huán)煙氣余熱的同時,將循環(huán)煙氣中的二惡英通過燃燒層裂解。該技術由荷蘭克魯斯艾莫伊登在其135m2燒結機上應用。
3.2環(huán)境型優(yōu)化燒結EPOSINT
EPOSINT工藝將機尾部分高溫度、高污染物濃度的煙氣引出,將35%的煙氣與冷卻機廢氣混合,用作循環(huán)氣使用,減排量達30%,但高硫循環(huán)煙氣使得燒結礦中含硫量增加。該技術由奧鋼聯(lián)鋼鐵公司應用于250m2燒結機上。
3.3低排放能量優(yōu)化燒結工藝LEEP
LEEP技術將燒結機后半部高溫度、高污染物濃度的煙氣與前半部分低溫煙氣換熱后進行循環(huán),循環(huán)比例達47%,SO2減排67.5%,二惡英減排90%,但同樣存在燒結礦含硫量增加,影響燒結礦品質的問題。技術由德國HKM公司在其420m2燒結機上應用。
3.4區(qū)域性廢氣循環(huán)技術
該技術將風箱分類,針對煙氣組分的區(qū)別進行不同的處理,將點火段高氧、低溫的煙氣循環(huán)至燒結機中段;低氧、低
SO2的煙氣經(jīng)除塵后排出;低氧、高SO2的煙氣引至脫硫設施處理;高氧、高SO2的煙氣經(jīng)換熱后循環(huán)至點火段后。此方法減排量可達28%,減排量相對較低,且改造復雜。由新日鐵公司在其480m2燒結機上使用。
4末端治理技術
4.1煙粉塵
國內(nèi)大部分燒結廠的煙氣除塵采用三電場或四電場的ESP,基本滿足脫硫入口煙氣粉塵含量達40~80mg/m3的要求。對于煙氣二次除塵,干法、半干法脫硫采用布袋除塵,濕法脫硫采用除霧器或濕法電除塵器(WESP)對煙粉塵進行控制。據(jù)統(tǒng)計75%以上的燒結ESP后煙粉塵濃度<50mg/m3。但ESP前后煙氣中PM2.5和PM10占煙粉塵總量的比重分別由51.23%升為93.13%和由43.73%升為85%。說明經(jīng)ESP后的煙粉塵主要為PM10,及更細的PM2.5。因此對煙氣中細顆粒物的脫除,是今后研究的主要方向。
4.2二氧化硫
目前燒結煙氣脫硫技術以濕法和半干法技術為主。截止至2012年,國內(nèi)脫硫設備共287套,其中濕法209套,占總數(shù)的
72.82%,以石灰(石)-石膏法為主;半干法76套,占總數(shù)的26.48%,主要為循環(huán)流化床法和旋轉噴霧法;干法2套,占總數(shù)的0.7%,為活性炭/焦法。
濕法脫硫技術的優(yōu)點是吸收劑利用率很高,脫硫效率在95%以上,對煙氣適用范圍寬,副產(chǎn)物脫硫石膏成分對穩(wěn)定,二次污染小。但工藝廢水中氯離子濃度高,對設備有定腐蝕;石灰漿液噴嘴易發(fā)生堵塞情況;除霧器易結垢堵塞,影響尾氣處理,形成石膏雨,對周邊環(huán)境造成污染。
半干法脫硫技術應用較多的有旋轉噴霧半干法、循環(huán)流化床法、MEROS等。半干法脫硫技術脫硫效率一般為85%~95%,具有同時脫除強酸、重金屬和二惡英的潛力,系統(tǒng)不存在腐蝕問題,適合處理煙氣溫度較高、SO2濃度較低的煙氣,基本無廢水排放,煙尾較輕,但副產(chǎn)物是以CaSO3為主的灰渣,用價值有限且易分解,產(chǎn)生二次污染。
干法,即活性炭/焦法,主要應用于太鋼和寶鋼湛江鋼鐵。優(yōu)點是吸附的SO2氣體可加工成硫酸,具有較高價值,且無二次污染。同時可實現(xiàn)脫硝、脫二惡英、吸附粉塵及重金屬等效果。但入塔煙氣SO2濃度不能超過2400mg/m3,以避免因吸附熱過高而發(fā)生爆炸。解析后產(chǎn)生的酸為混合酸,要求設備防腐性能高,而且投資及運行費用高。
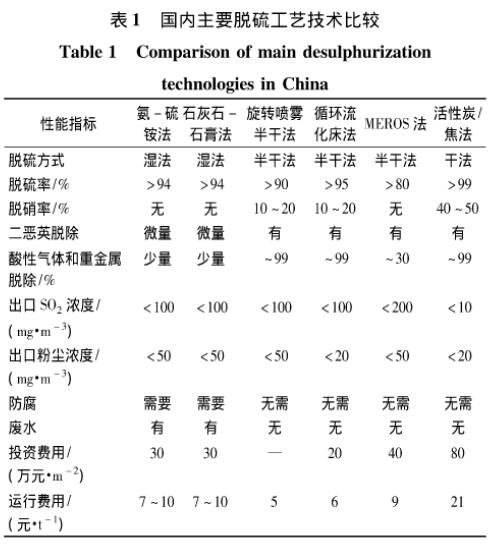
4.3氮氧化物
燒結煙氣脫硝工藝應用的僅有活性炭/焦吸附技術。中、低溫選擇性催化還原技術(SCR)尚未普及。
活性炭/焦技術是利用活性炭/焦對NOx的吸附催化作用,脫氮效率約50%。
中溫SCR工藝是在300℃以上,利用氨或尿素等與NOx反應生成N2,脫硝效率可達80%,但由于燒結煙氣溫度僅為80~180℃,加熱耗能巨大,且SCR技術投資大,因此經(jīng)濟適用性較差。目前,應用該技術的有日本Kawasaki鋼鐵公司Chiba廠,Kokan公司的Keihin廠,中國臺灣中鋼3、4號燒結機。
低溫SCR工藝的溫度窗口在120~300℃,無需加熱煙氣。但在低溫下,SO2與H2O、NH3易形成黏稠的銨鹽,使催化劑中毒失活。因此,低溫SCR需對入口煙氣的粉塵和SO2濃度進行嚴格控制。目前,低溫SCR催化劑分為釩鈦體系和非釩系(錳基系為主)兩種。尚無工程應用。
4.4二惡英
煙氣中二惡英控制主要方法為活性炭/焦法,可將被吸附的二惡英分解為CO2、H2O、HCl。太鋼的活性炭工藝可控制二惡英濃度達到約0.12ng-TEQ/m3。
還有的工藝是在布袋除塵器前加噴碳裝置,活性炭在煙道里吸附二惡英,并通過除塵器脫除。吸附了二惡英的活性炭可添加到燒結料中。該工藝國內(nèi)報道較少,脫除效果有待進一步研究。
4.5多污染物聯(lián)合防治
單一污染物的治理技術難以滿足新標準中多污染物排放限值要求。因此,聯(lián)合防治、優(yōu)化組合是未來燒結煙氣治理的發(fā)展方向。
4.5.1ESP+GGH+SCR+WFGD法
該技術路線主要針對WFGD的改造。將SCR系統(tǒng)放在脫硫前,通過換熱器GGH提高煙氣溫度來滿足SCR系統(tǒng)要求。整個系統(tǒng)具有脫硫、脫硝、脫二惡英的多污染物處理能力。但需要注意SCR系統(tǒng)催化劑中毒問題。
4.5.2ESP+一體化脫硫脫硝+FB法
一體化脫硫脫硝是指在脫硫塔中加入催化劑使其具有同時脫硫脫硝的效果。但由于以半干法脫硫工藝為基礎,所以主要適用于SO2濃度小于2000mg/m3煙氣。
4.5.3ESP+活性炭/焦法
活性炭/焦法本身具有多污染物脫除效果,符合多污染物聯(lián)合防治的發(fā)展方向,副產(chǎn)品可有效利用,但不適合處理SO2濃度高或波動大的煙氣,且投資和運行費用較高。
4.5.4ESP+WFGD+WESP法
在濕法脫硫后面加上濕法電除塵,可以進一步提高脫硫能力,并實現(xiàn)煙粉塵的超低排放。其次,WESP具有一定的脫除重金屬、NOx脫除能力,但具體脫除效果仍需進步研究。
5總結
1)目前,燒結ESP在正常運行時,可滿足煙粉塵排放標準,但需要針對PM10和PM2.5研究高效脫除技術;脫硫工藝較成熟,但如何安全有效利用脫硫副產(chǎn)物,減少環(huán)境二次污染是其研究的主要方向;脫硝工藝尚不成熟,關鍵是如何適應整個燒結煙氣凈化系統(tǒng),以及開發(fā)低溫抗硫的催化劑;二惡英的脫除尚無成熟工藝,源頭抑制技術有待進一步研究。
2)新標準中對多種污染物設定了排放限值,這意味著燒結煙氣治理應向著多污染物聯(lián)合防治的方向發(fā)展,形成一體化脫除技術或優(yōu)化多項工藝后的聯(lián)合凈化系統(tǒng)。并選擇技術可靠、經(jīng)濟效益與環(huán)境效益相協(xié)調的工藝路線,減輕鋼鐵企業(yè)的環(huán)保負擔。
3)燒結煙氣中的有害重金屬會被富集在燒結礦、細顆粒物和脫硫副產(chǎn)物中,影響高爐生產(chǎn)和凈化設備副產(chǎn)物的二次利用;細顆粒物會隨著煙氣外排、沉降,污染周邊環(huán)境。目前,對重金屬的研究主要集中在汞的去除,但燒結煙氣中Pb、Zn、As等重金屬的含量更高,應及早展開相關重金屬治理的研究。
來源:《環(huán)境工程》 作者:張璞 王琿等
特此聲明:
1. 本網(wǎng)轉載并注明自其他來源的作品,目的在于傳遞更多信息,并不代表本網(wǎng)贊同其觀點。
2. 請文章來源方確保投稿文章內(nèi)容及其附屬圖片無版權爭議問題,如發(fā)生涉及內(nèi)容、版權等問題,文章來源方自負相關法律責任。
3. 如涉及作品內(nèi)容、版權等問題,請在作品發(fā)表之日內(nèi)起一周內(nèi)與本網(wǎng)聯(lián)系,否則視為放棄相關權益。