目前我國電源結(jié)構(gòu)仍然是以燃煤火力發(fā)電為主,2015年全國總發(fā)電量為57399億千瓦時,其中燃煤火電機組發(fā)電量為38977億千瓦,占總發(fā)電總量的67.9%[1]。燃煤電廠脫硫技術(shù)大多數(shù)采用石灰石-石膏法煙氣脫硫技術(shù)(FGD法),F(xiàn)GD法具有脫硫效率高(大于90%,可達(dá)97%)、運行可靠(大于95%)、適應(yīng)范圍廣、技術(shù)成熟、附產(chǎn)物可出售等優(yōu)勢。
這種濕法脫硫工藝為了維持脫硫系統(tǒng)的正常運行,漿液中氯離子與微細(xì)粉塵的濃度需維持在一定水平:為防止脫硫系統(tǒng)材料的腐蝕,漿液氯離子濃度一般維持在12000~20000mg/kg[2];為維持較高的脫硫效率及防止塔體結(jié)垢,漿液密度一般控制在1075~1150kg/m3[3],因此必須從脫硫系統(tǒng)中排出一定量的廢水,從而保證FGD系統(tǒng)安全可靠性的運行。
脫硫系統(tǒng)排出的廢水,其pH為4~6,同時含有大量的懸浮物(石膏顆粒、SiO2、Al和Fe的氫氧化物)、氟化物和微量的重金屬,如As、Cd、Cr、Hg等[4],如果廢水直接排放將對環(huán)境造成嚴(yán)重危害,因此這部分廢水經(jīng)處理后一般用于干灰調(diào)濕或者灰場噴灑。
隨著《水污染防治行動計劃》(水十條)的頒布及脫硫廢水“零排放”(ZeroLiquidDisge,ZLD)概念的提出,盡可能回用脫硫廢水并回收廢水中的有用資源,是火力發(fā)電廠脫硫廢水系統(tǒng)研究的一個重要方向。
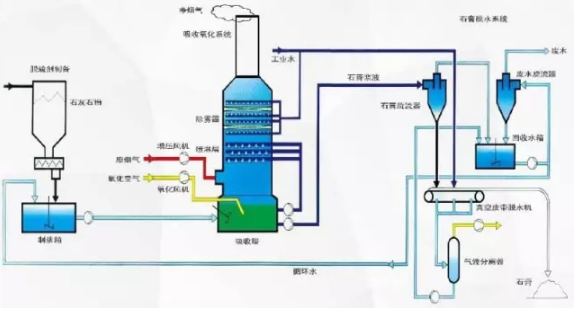
圖1石灰石-石膏法脫硫工藝脫硫廢水來源
1、傳統(tǒng)脫硫廢水處理工藝
脫硫廢水的傳統(tǒng)處理工藝主要以化學(xué)處理為主,其處理系統(tǒng)可分為廢水處理系統(tǒng)和污泥處理系統(tǒng)。廢水處理系統(tǒng)又可分為預(yù)處理、減量濃縮和固化等工序。
(1)預(yù)處理單元:在中和水箱中加入5%左右的石灰乳溶液,將脫硫廢水的pH值提高至9.0以上,使大多數(shù)重金屬離子在堿性環(huán)境中生成難溶的重金屬氫氧化物并沉淀,原脫硫廢水中的懸浮物(SS)也會沉淀去除。
(2)濃縮減量單元:脫硫廢水中加入石灰乳溶液后,當(dāng)pH為9.0~9.5時,溶液中的Ca2+與廢水中的部分F-反應(yīng),生成難溶的CaF2,從而達(dá)到去除氟的目的。但經(jīng)中和處理后的廢水中Pb2+、Hg2+含量仍然超標(biāo),因此,在沉降箱中加入有機硫化物(TMT15),使其與殘余的離子態(tài)的Pb2+、Hg2+反應(yīng)并生成難溶的硫化物并且沉淀。
脫硫廢水中的懸浮物含量較大,設(shè)計值為6000~12000mg/L,脫硫廢水中的懸浮物主要成分為石膏顆粒、SiO2、Fe和Al的氫氧化物。采用絮凝方法使膠體顆粒和懸浮物顆粒發(fā)生凝聚和聚集,從液相中分離,是一種降低懸浮物的有效方法。
因此在絮凝箱中加入絮凝劑FeClSO4,使其中的小顆粒凝聚成大顆粒從而沉積,并且在澄清池入口加入聚丙烯酰胺(PAM)來進(jìn)一步強化凝聚過程,使絮凝體更容易沉積下來。
(3)固化單元:絮凝后的廢水從反應(yīng)池溢流進(jìn)入澄清池中,絮凝物沉積在底部濃縮成污泥,上部則為系統(tǒng)出水。大部分污泥經(jīng)泵排至板框式壓濾機,小部分污泥返回中和反應(yīng)箱,提供絮凝體形成所需的晶核。
上部出水溢流到出水箱,出水箱設(shè)置了監(jiān)測出水pH和濁度的在線監(jiān)測儀表,如果pH和濁度達(dá)到排水設(shè)計標(biāo)準(zhǔn),則通過出水泵外排,否則將加酸調(diào)節(jié)pH或?qū)⑵渌突刂泻拖淅^續(xù)處理,直到合格為止。
2脫硫廢水“零排放”處理工藝
廢水“零排放”(ZeroLiquidDisge,ZLD)一般是指電廠不向外部水域排放任何廢水,所有離開電廠的水都是以蒸汽的形式蒸發(fā)到大氣中,或是以少量的水分包含在灰和渣中[5]。目前主流的脫硫廢水“零排放”處理工藝主要有以下三種方法。
2.1蒸發(fā)法
蒸發(fā)法是廢水“零排放”處理中常用的方法之一,該工藝也被應(yīng)用于脫硫廢水的處理中。蒸發(fā)法的基本原理是:進(jìn)入蒸發(fā)器的廢水通過蒸汽或電熱器加熱至沸騰,廢水中的水分逐漸蒸發(fā),水蒸氣經(jīng)冷卻后重新凝結(jié)成水而重復(fù)利用,廢水中的溶解性固體被截留在殘液中,隨著濃縮倍數(shù)的提高,最終以晶體形式析出。蒸發(fā)法已廣泛應(yīng)用于化工領(lǐng)域,既可以單獨使用,也可以與其他工藝聯(lián)合使用。

圖2傳統(tǒng)脫硫廢水處理工藝流程圖
隨著近年來水處理技術(shù)的不斷進(jìn)步,蒸發(fā)法中的多效蒸發(fā)工藝得到快速發(fā)展,因其具有傳熱系數(shù)高、操作彈性大、進(jìn)水預(yù)處理簡單和能耗相對較低的優(yōu)點,被廣泛應(yīng)用于化工、醫(yī)藥、海水淡化以及廢水處理等領(lǐng)域中。
在實際應(yīng)用方面,廣東河源電廠采用化學(xué)沉淀+多效蒸發(fā)結(jié)晶組合處理工藝處理脫硫廢水。
具體工藝流程為:廢水首先經(jīng)過化學(xué)沉淀法預(yù)處理,澄清池出水進(jìn)入多效蒸發(fā)結(jié)晶處理系統(tǒng)。該工程于2009年完成調(diào)試驗收并投入商業(yè)運行,系統(tǒng)處理能力為22t/h。經(jīng)過上述工藝處理后,產(chǎn)生的結(jié)晶鹽滿足二級工業(yè)鹽標(biāo)準(zhǔn),其不足之處在于系統(tǒng)能耗和運行成本高[6],系統(tǒng)建設(shè)需要的場地大。
2.2膜法過濾類工藝
由于脫硫廢水“零排放”對水鹽分離程度要求很高,通常采用多重反滲透過濾工藝。反滲透工藝首先需要經(jīng)過預(yù)處理,反滲透預(yù)處理工藝以膜過濾為主,輔以殺菌工藝和沉淀工藝,目的是去除水中的懸浮物和微生物,使處理后的水質(zhì)能夠初步滿足反滲透的進(jìn)水要求。
主體工藝通常采用兩段反滲透系統(tǒng),由于二段系統(tǒng)的進(jìn)水為一段系統(tǒng)的濃水,需用專門的化學(xué)藥劑對其進(jìn)行處理,以確保二段系統(tǒng)的進(jìn)水參數(shù)符合要求。同時在其進(jìn)入二段系統(tǒng)前,可針對其水質(zhì)情況,添加專業(yè)的阻垢劑和調(diào)節(jié)劑,確保系統(tǒng)穩(wěn)定運行。產(chǎn)品水進(jìn)入回用水池,系統(tǒng)中少量的濃水可用來沖渣,實現(xiàn)水處理系統(tǒng)的“零排放”。
神華億利煤矸石電廠高效反滲透廢水處理工藝系統(tǒng)主要采用“石灰軟化+過濾+離子交換+反滲透”的處理工藝,主要包括廢水收集和輸送系統(tǒng)、預(yù)處理系統(tǒng)、離子交換系統(tǒng)、反滲透系統(tǒng)、RO濃水回用系統(tǒng)、加藥系統(tǒng)、壓縮空氣系統(tǒng)。該廠使用了美國PROC-10S反滲透膜元件,反滲透進(jìn)水pH基本維持在8~9之間,系統(tǒng)運行較為穩(wěn)定。
Ca2+、Mg2+、Fe3+等在預(yù)處理階段已得到了較好的控制,且總回收率和脫鹽率均達(dá)95%左右,基本實現(xiàn)了“零排放”[7]。

圖3神華億利煤矸石電廠高效反滲透廢水處理工藝流程
2.3煙道處理法
2.3.1處理工藝
煙道處理法是在煙道內(nèi)對廢水進(jìn)行噴霧蒸發(fā)處理的一種方法。噴霧蒸發(fā)法在食品、化工等領(lǐng)域應(yīng)用廣泛,但在廢水處理中應(yīng)用較少。采用煙道蒸發(fā)法處理脫硫廢水時,首先采用一定的噴射方式將脫硫廢水霧化后噴入電除塵器之前的煙道內(nèi)[8],廢水以小液滴的形式經(jīng)過高溫?zé)煔饧訜岷笱杆僬舭l(fā)氣化,其中的懸浮物和可溶性固體形成細(xì)小固體顆粒,然后在氣流的夾帶作用下進(jìn)入電除塵器并被電極捕捉去除,最終實現(xiàn)脫硫的廢水近零排放處理。處理系統(tǒng)主要由預(yù)處理單元,減量化單元和固化單元三部分組成。
預(yù)處理單元:通過向反應(yīng)箱中投加石灰乳、碳酸鈉和堿液等藥劑去除水中的硬度離子、懸浮物等,減小其沉淀時間。絮凝后溶液中包含的絡(luò)合物、沉淀物以及SS積聚成的大顆粒物被送至固液分離器,實現(xiàn)固液分離。
減量化單元:預(yù)處理系統(tǒng)的出水在水箱收集,用鹽酸調(diào)節(jié)pH至中性,輸送至微濾系統(tǒng)。預(yù)處理及微濾系統(tǒng)可有效去除水中的固體微粒雜質(zhì),降低除鹽模塊負(fù)荷、延長反滲透膜的使用壽命,微濾出水進(jìn)入反滲透系統(tǒng),系統(tǒng)產(chǎn)淡水60%以上回收利用,40%的濃水進(jìn)入煙道蒸發(fā)結(jié)晶。
反滲透濃水進(jìn)入煙道蒸發(fā)器系統(tǒng),采用霧化噴嘴將其霧化,噴入電除塵器和空預(yù)器之間的煙道蒸發(fā)器,利用煙道內(nèi)的高溫余熱煙氣將霧化后的濃水蒸發(fā)為水蒸汽,蒸汽隨除塵器后的煙氣進(jìn)入脫硫塔,在脫硫塔的噴淋冷卻作用下,水分凝結(jié)進(jìn)入脫硫塔的漿液循環(huán)系統(tǒng);蒸發(fā)結(jié)晶物隨灰塵一起進(jìn)入電除塵器隨灰分外排。
固化單元:固化單元指將反滲透的濃水蒸發(fā)為水蒸汽,使其中的鹽分結(jié)晶成為固態(tài)鹽品。采用反滲透處理工藝后的濃水,結(jié)晶鹽可以作為工業(yè)鹽銷售。
2.3.2工藝要求
煙道直接霧化法的工藝要求:
1)煙道霧化蒸發(fā)煙氣溫度不低于110℃。
2)需要直管段煙道不小于9m。
3)煙氣溫度越低,蒸發(fā)水量越少,因此需機組負(fù)荷應(yīng)盡量穩(wěn)定。
4)目前適用于靜電和電袋除塵器,布袋除塵器不適用。
2.3.3工藝優(yōu)勢
與現(xiàn)行脫硫廢水處理技術(shù)相比,煙道處理法具有以下優(yōu)點,包括:
1)處理設(shè)備簡單,可以有效克服現(xiàn)有脫硫廢水處理系統(tǒng)設(shè)備多、投資大、運行成本高和設(shè)備檢修維護(hù)工作量大的缺點。
2)操作簡單,廢水中的污染物以灰分形式排出。
3)由于廢水向煙道內(nèi)引入,可以適當(dāng)提高煙氣濕度,從而降低煙氣中灰塵顆粒的比電阻,有利于提高除塵效率。

圖4煙道處理法工藝流程圖
3三種“零排放”技術(shù)經(jīng)濟(jì)對比
本次選取國內(nèi)已投運的脫硫廢水“零排放”項目,項目采用不同的脫硫廢水“零排放”處理方案,其技術(shù)經(jīng)濟(jì)對比見表1。
表1三種“零排放”技術(shù)經(jīng)濟(jì)對比表

由表1可知,三種脫硫廢水“零排放”處理技術(shù)中,蒸發(fā)法投資最大,運行費用最高,占地也最大;膜處理工藝法投資較大,運行費用較高,占地較大;煙道蒸發(fā)處理法投資最少,運行費用最少,占地也最小。
4結(jié)論
通過對上述三種脫硫廢水“零排放”方案比選和研究可知,建設(shè)項目脫硫廢水“零排放”處理方案選擇時應(yīng)根據(jù)項目自身建設(shè)條件及其他限制條件,綜合考慮后選擇符合項目建設(shè)最合理和經(jīng)濟(jì)的方案。
來源:《環(huán)境與發(fā)展》 作者:杜樂等
特此聲明:
1. 本網(wǎng)轉(zhuǎn)載并注明自其他來源的作品,目的在于傳遞更多信息,并不代表本網(wǎng)贊同其觀點。
2. 請文章來源方確保投稿文章內(nèi)容及其附屬圖片無版權(quán)爭議問題,如發(fā)生涉及內(nèi)容、版權(quán)等問題,文章來源方自負(fù)相關(guān)法律責(zé)任。
3. 如涉及作品內(nèi)容、版權(quán)等問題,請在作品發(fā)表之日內(nèi)起一周內(nèi)與本網(wǎng)聯(lián)系,否則視為放棄相關(guān)權(quán)益。